RETIRED - SparkFun Inventor's Kit Experiment Guide - v4.0
This Tutorial is Retired!
This tutorial covers concepts or technologies that are no longer current. It's still here for you to read and enjoy, but may not be as useful as our newest tutorials.
View the updated tutorial: SparkFun Inventor's Kit Experiment Guide - v4.0
Circuit 5A: Motor Basics
In this circuit you will learn the basic concepts behind motor control. Motors require a lot of current, so you can’t drive them directly from a digital pin on the RedBoard. Instead, you’ll use what is known as a motor controller or motor driver board to power and spin the motor accordingly.
Parts Needed
Grab the following quantities of each part listed to build this circuit:
New Components
Switch
A switch is a component that controls the open-ness or closed-ness of an electric circuit. Just like the momentary buttons used in earlier circuits, a switch can only exist in one of two states: open or closed. However, a switch is different in that it will stay in the position it was last in until it is switched again.
DC Gearmotors
The motors in your Inventor’s Kit have two main parts: a small DC motor that spins quickly and a plastic gearbox that gears down that output from the hobby motor so that it is slower but stronger, allowing it to move your robot. The motors have a clever design so that you can attach things that you want to spin fast (like a small fan or flag) to the hobby motor, and things that you want to be strong (like a wheel) to the plastic axle sticking out the side of the motor. The included wheels just so happen to fit on the plastic axles.
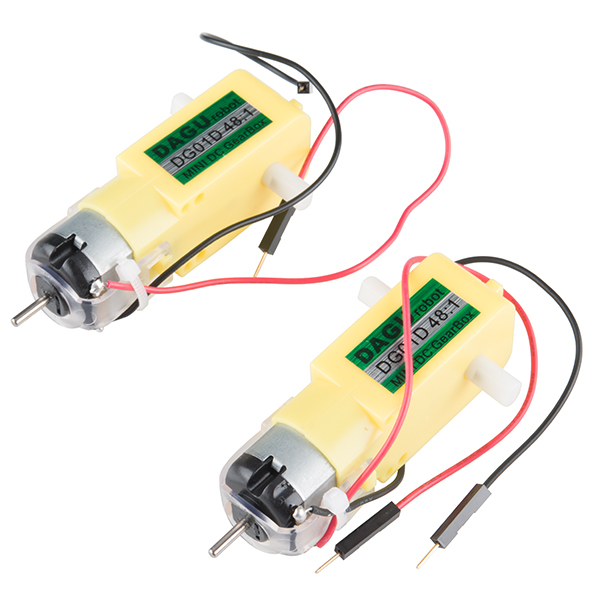

Inside the hobby motor are coils of wire that generate magnetic fields when electricity flows through them. When power is supplied to these electromagnets, they spin the drive shaft of the motor.
TB6612FNG Motor Driver
If you switch the direction of current through a motor by swapping the positive and negative leads, the motor will spin in the opposite direction. Motor controllers contain a set of switches (called an H-bridge) that let you easily control the direction of one or more motors. The TB6612FNG Motor Driver takes commands for each motor over three wires (two wires control direction, and one controls speed), then uses these signals to control the current through two wires attached to your motor.
New Concepts
Voltage In (VIN)
This circuit utilizes the VIN pin found with the other power pins. The VIN pin outputs a voltage that varies based on whatever voltage the RedBoard is powered with. If the RedBoard is powered through the USB port, then the voltage on VIN will be about 4.6--5V. However, if you power the RedBoard through the barrel jack (highlighted in the picture below), the VIN pin will reflect that voltage. For example, if you were to power the barrel jack with 9V, the voltage out on VIN would also be 9V.
Integrated Circuits (ICs) and Breakout Boards
An Integrated Circuit (IC) is a collection of electronic components --- resistors, transistors, capacitors, etc. --- all stuffed into a tiny chip and connected together to achieve a common goal. They come in all sorts of flavors, shapes and sizes. The chip that powers the RedBoard, the ATMega328, is an IC. The chip on the motor driver, the TB6612FNG, is another IC, one designed to control motors, referred to as an H-bridge.
Integrated circuits are often too small to work with by hand. To make working with ICs easier and to make them breadboard-compatible, they are often added to a breakout board, which is a printed circuit board that connects all the IC's tiny legs to larger ones that fit in a breadboard. The motor driver board in your kit is an example of a breakout board.
Hardware Hookup
Polarized Components | Pay special attention to the component’s markings indicating how to place it on the breadboard. Polarized components can only be connected to a circuit in one direction. |
Most ICs have polarity and usually have a polarity marking in one of the corners. The motor driver is no exception. Be sure to insert the motor driver as indicated in the circuit diagrams. The motor driver pins are shown in the image below.
Each pin and its function is covered in the table below.
Pin Label | Function | Power/Input/Output | Notes |
---|---|---|---|
VM | Motor Voltage | Power | This is where you provide power for the motors (2.2V to 13.5V) |
VCC | Logic Voltage | Power | This is the voltage to power the chip and talk to the microcontroller (2.7V to 5.5V) |
GND | Ground | Power | Common Ground for both motor voltage and logic voltage (all GND pins are connected) |
STBY | Standby | Input | Allows the H-bridges to work when high (has a pulldown resistor so it must actively be pulled high) |
AIN1/BIN1 | Input 1 for channels A/B | Input | One of the two inputs that determines the direction |
AIN2/BIN2 | Input 2 for channels A/B | Input | One of the two inputs that determines the direction |
PWMA/PWMB | PWM input for channels A/B | Input | PWM input that controls the speed |
A01/B01 | Output 1 for channels A/B | Output | One of the two outputs to connect the motor |
A02/B02 | Output 2 for channels A/B | Output | One of the two outputs to connect the motor |
When you're finished with Project 5, removing the motor driver from the breadboard can be difficult due to its numerous legs. To make this easier, use the included screwdriver as a lever to gently pry it out. Be careful not to bend the legs as you remove it.
The motors are also polarized. However, motors are unique in that they will still work when the two connections are reversed. They will just spin in the opposite direction when hooked up backward. To keep things simple, always think of the red wire as positive ( + ) and the black wire as negative ( - ).
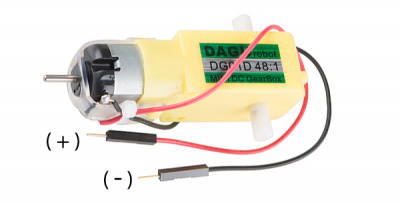
Last, the switch is not polarized. It works the same no matter its orientation.
Ready to start hooking everything up? Check out the circuit diagram and hookup table below to see how everything is connected.
Circuit Diagram
Hookup Table
Component | RedBoard | Breadboard | Breadboard | Breadboard |
---|---|---|---|---|
Jumper Wire | 5V | 5V Rail ( + ) | ||
Jumper Wire | GND | GND Rail ( - ) | ||
Jumper Wire | 5V Rail ( + ) | 5V Rail ( + ) | ||
Jumper Wire | GND Rail ( - ) | GND Rail ( - ) | ||
Jumper Wire | VIN | A1 | ||
Motor Driver | C1-C8 (VM on C1) | G1-G8 (PWMA on G1) | ||
Jumper Wire | A2 | 5V Rail ( + ) | ||
Jumper Wire | A3 | GND Rail ( - ) | ||
Jumper Wire | Digital Pin 8 | J7 | ||
Jumper Wire | Digital Pin 9 | J6 | ||
Jumper Wire | Digital Pin 10 | J5 | ||
Jumper Wire | J4 | 5V Rail ( + ) | ||
Jumper Wire | Digital Pin 11 | J3 | ||
Jumper Wire | Digital Pin 12 | J2 | ||
Jumper Wire | Digital Pin 13 | J1 | ||
Motor | A4 (Red +) | A5 (Black -) | ||
Switch | F25 | F26 | F27 | |
Jumper Wire | I26 | GND Rail ( - ) | ||
Jumper Wire | Digital Pin 7 | I27 |
Open the Sketch
To open the code, go to: File > Examples > SIK_Guide_Code-V_4 > SIK_Circuit_5A-MotorBasics.
You can also copy and paste the following code into the Arduino IDE. Hit upload, and see what happens!
language:cpp
/*
SparkFun Inventor’s Kit
Circuit 5A - Motor Basics
Learn how to control one motor with the motor driver.
This sketch was written by SparkFun Electronics, with lots of help from the Arduino community.
This code is completely free for any use.
View circuit diagram and instructions at: https://learn.sparkfun.com/tutorials/sparkfun-inventors-kit-experiment-guide---v40
Download drawings and code at: https://github.com/sparkfun/SIK-Guide-Code
*/
//PIN VARIABLES
//the motor will be controlled by the motor A pins on the motor driver
const int AIN1 = 11; //control pin 1 on the motor driver for the right motor
const int AIN2 = 12; //control pin 2 on the motor driver for the right motor
const int PWMA = 13; //speed control pin on the motor driver for the right motor
int switchPin = 7; //switch to turn the robot on and off
//VARIABLES
int motorSpeed = 0; //starting speed for the motor
void setup() {
pinMode(switchPin, INPUT_PULLUP); //set this as a pullup to sense whether the switch is flipped
//set the motor contro pins as outputs
pinMode(AIN1, OUTPUT);
pinMode(AIN2, OUTPUT);
pinMode(PWMA, OUTPUT);
Serial.begin(9600); //begin serial communication with the computer
Serial.println("Enter motor speed (255, 0, or -255)... "); //Prompt to get input in the serial monitor.
}
void loop() {
if (Serial.available() > 0){ //if the user has entered something in the serial monitor
motorSpeed = Serial.parseInt(); //set the motor speed equal to the number in the serial message
Serial.print("Motor Speed: "); //print the speed that the motor is set to run at
Serial.println(motorSpeed);
}
if(digitalRead(7) == LOW){ //if the switch is on...
spinMotor(motorSpeed);
} else{ //if the switch is off...
spinMotor(0); //turn the motor off
}
}
/********************************************************************************/
void spinMotor(int motorSpeed) //function for driving the right motor
{
if (motorSpeed > 0) //if the motor should drive forward (positive speed)
{
digitalWrite(AIN1, HIGH); //set pin 1 to high
digitalWrite(AIN2, LOW); //set pin 2 to low
}
else if (motorSpeed < 0) //if the motor should drive backwar (negative speed)
{
digitalWrite(AIN1, LOW); //set pin 1 to low
digitalWrite(AIN2, HIGH); //set pin 2 to high
}
else //if the motor should stop
{
digitalWrite(AIN1, LOW); //set pin 1 to low
digitalWrite(AIN2, LOW); //set pin 2 to low
}
analogWrite(PWMA, abs(motorSpeed)); //now that the motor direction is set, drive it at the entered speed
}
What You Should See
When you flip the switch, the motor will turn on and spin at the speed set by the motor speed variable (default is 0). By opening the serial monitor and sending numbers, you can change the speed of the motor. Any number from about 130 to 255 or -130 to -255 will work, though changes in the speed will be hard to notice. Send the number 0 to stop the motor. Adding a piece of tape to the motor shaft makes it easier to see it spinning.
Program Overview
- Check to see if a command has been sent through the Serial Monitor. If a command has been sent, then set the motor speed to the number that was sent over the Serial Monitor.
- Check to see if the switch is ON or OFF. a. If the switch is ON, drive the motor at the motor speed. b. If the switch is OFF, stop the motor.
Code to Note
Code | Description |
---|---|
Parsing Integers:Serial.parseInt(); | parseInt() receives integer numbers from the serial monitor. It returns the value of the number that it receives, so you can use it like a variable. |
Serial Available:Serial.available(); | Serial.available() checks how many bytes of data are being sent to the RedBoard. If it is greater than 0, then a message has been sent. It can be used in an if statement to run code only when a command has been received. |
Coding Challenges
Challenge | Description |
---|---|
Make the switch change directions | Change the code so that the position of the switch changes the direction of the motor instead of turning it on and off. |
Replace the switch with a button | Try wiring a button into the circuit instead of the sliding switch. Now the motor only turns on when you push the button. |
Replace the switch with a sensor | Try changing the code so that the motor is activated by another sensor, like the photoresistor. |
Troubleshooting
Problem | Solution |
---|---|
Motor not spinning | Check the wiring to the motor driver. There are a lot of connections, and it’s easy to mix one of them up with another. If it is still not working, you can test the B channel by moving you motor. (Black wire to A6, Red wire to A7). You’ll need to change the code as well. |
Switch not working | Make sure that you are hooked up to the middle pin and one side pin on the switch. |
Still not working? | Jumper wires unfortunately can go "bad" from getting bent too much. The copper wire inside can break, leaving an open connection in your circuit. If you are certain that your circuit is wired correctly and that your code is error-free and uploaded but you are still encountering issues, try replacing one or more of the jumper wires for the component that is not working. |